プラスティックゴミをリサイクルするprecious plastic のバージョン4が発表されてもう2ヶ月。
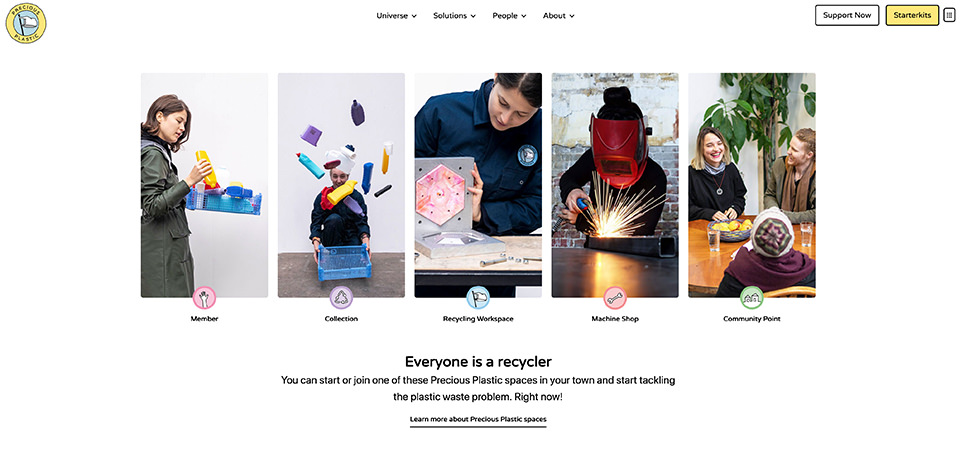
バージョン4にはpro版となる大型シュレッダーの設計図も公開されており、すっごい性能高そうだけど、いかんせんでかい。そして高価。(モーターなんて400V / 4kW推奨ですぜ!)
そこで今日は、ダイナミックラボアレンジの高性能かつ安価なシュレッダーを開発しましたよ! という話。
この記事は、既存のprecious plastic shredder V2をより高効率に改造したよ、というお話です。そもそも最初から高性能なダイナミックラボverも近日中に公開予定!
事の発端。ダイナミックラボのシュレッダー、実は破砕能力が低かった
鹿児島市内の鉄工屋さんに作ってもらったものの、、、
2016年に、鹿児島市内の鉄工屋さんに頼んで作ってもらったおそらく日本初のprecious plastic シュレッダー。モーターは 100V / 750W、減速比45のご家庭仕様(ヤフオクで5000円だった)
当初は私が機械のことをまるでわかっていなかったので「こういうもんだ」と思っていたものの、3年半の時を経て私の機械や精度に対する理解が深まるにつれて、段々と気づいたのでした。
これ、なんか違う!
どうやら当時製作した方(組み立て者)の破砕に対する理解が浅いために、不具合に対して対処療法を重ね、公式とは違うものができあがり、しょっちゅうプラ破砕片が詰まってモーターが止まる(jamming)事態に。
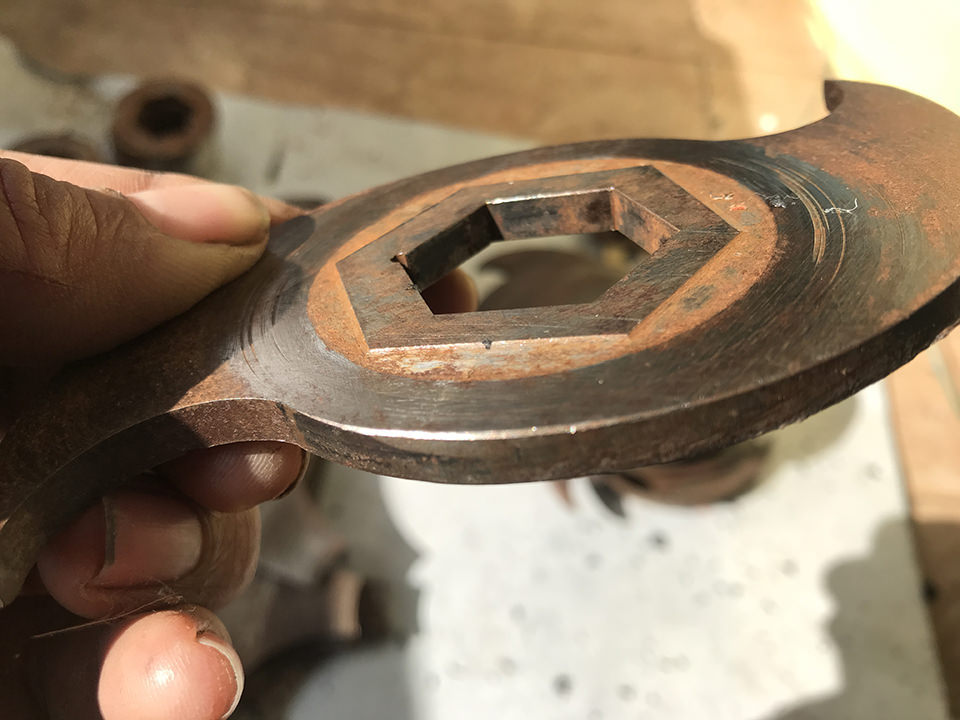
いやー、どうしたものか。
そうこうしているうちに、公式のprecious plastic からバージョン4のプロ版シュレッダーが発表される
時を同じくして、2020年1/7に公式からバージョン4が発表されるとのことで、それならバージョン4のシュレッダーを新たに作ろうと思い、1/7を指折り数える日々。
そして1/7に発表されたバージョン4のシュレッダーPRO!
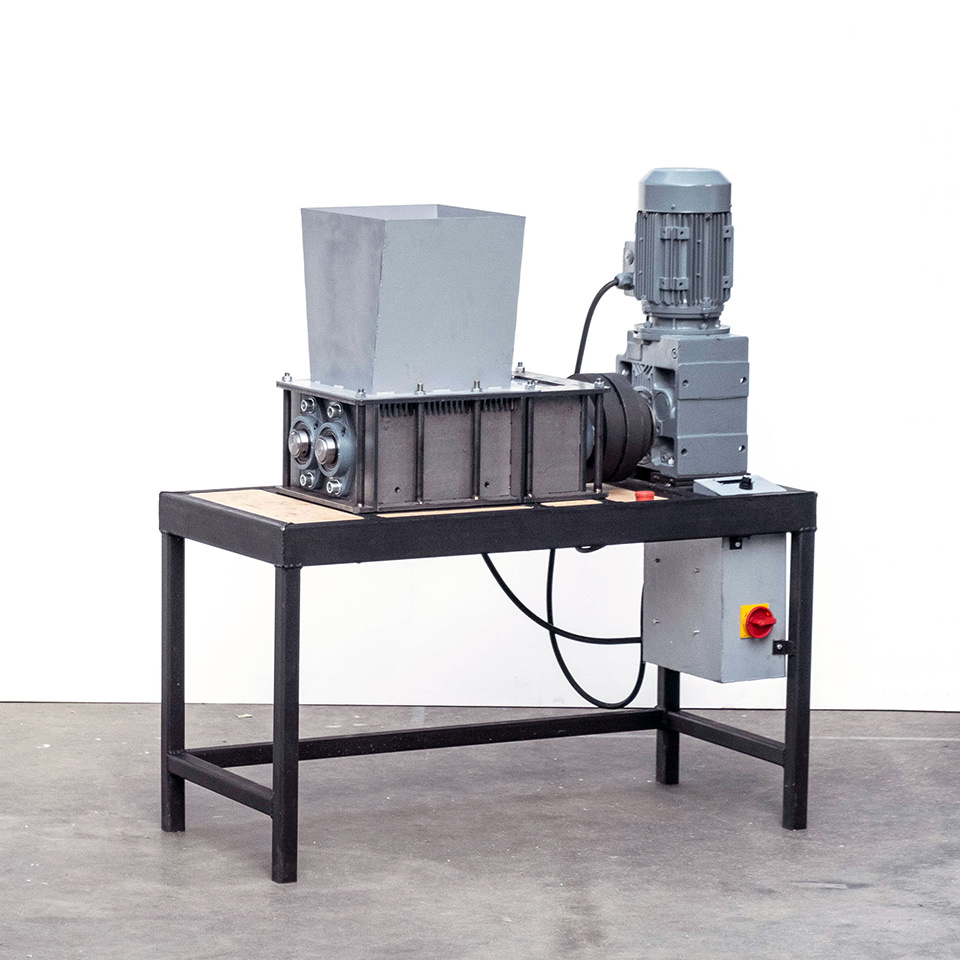
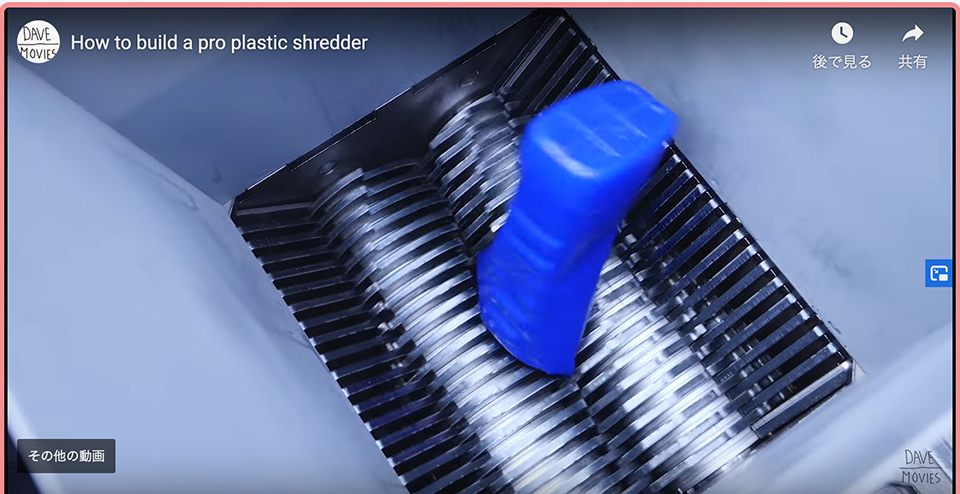
2軸になってめっちゃカッコいい・・・ものの、高価かつ複雑で、製作のためには高性能な機械の使用が前提となっているのでした。公式の見積もりによるとモーター以外で20万円以上かかるとのこと。
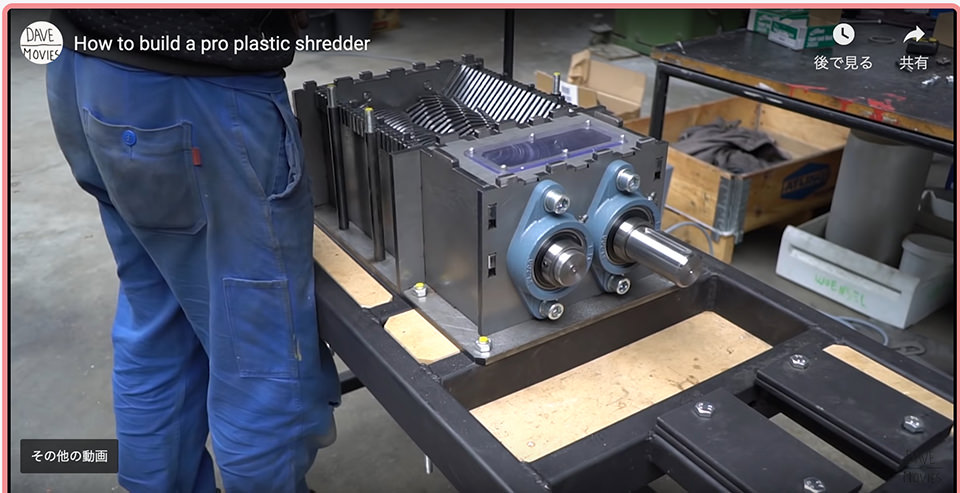
というわけでよく考えること数日。
- 実際には、高性能なものが一台あるよりかは、取り回しのいい小さなものが数台あって、プラスチックの材料ごとに使い分けられる方が便利。
- かつ、うちの運用では、ものすごくでかいものを砕くことはない。
と結論を出して、オリジナルアレンジの安価で詰まらないもの(つまらないものですが!)を作ることに決定!
そもそもの precious plastic シュレッダーの設計を見直す
改造している人がすでにいるのでは?と思ってウェブで(英語で)探して見つけた、私が見た限りでは一番観察を深めていたPDFがこちら(やっぱり英語)
Development of a Plastic Shredder / Rasmus Ekman
http://lup.lub.lu.se/luur/download?func=downloadFile&recordOId=8938831&fileOId=8938833
最終的にはかなりスペイシーな解決案までいってしまうのだけど、まずはその中からすぐに取り掛かれそうで効果のありそうなポイントを2つ選んだ。
1. 回転刃(ブレードナイフ)の形状変更
Ekmanさんの指摘を読んで「言われてみれば、そりゃそうだな…!」と思ったポイントその1がこれ。
回転軸に近ければ近いほど剪断力は上がるので、公式の出している円弧型のブレードナイフでは、プラごみがナイフの円弧中央に集まってしまうのでロスがある。よって円弧ではなく直線形状のブレードの方が良い。
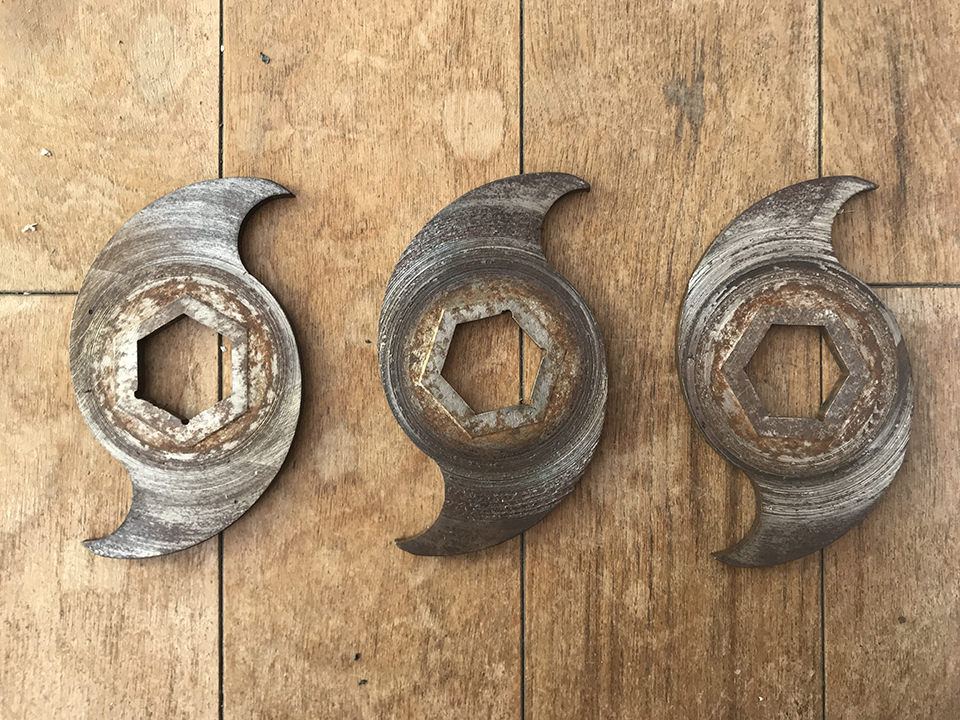
イメージ的には円弧の方がプラゴミを噛みそう(引き込みそう)だけど、たぶんあまり関係ない。というわけで直線ブレードナイフでやってみよう。
ブレードナイフを直線に変えるのは、直線ブレードナイフの図面を書いて、レーザーカットに発注出すだけなので、割合簡単。
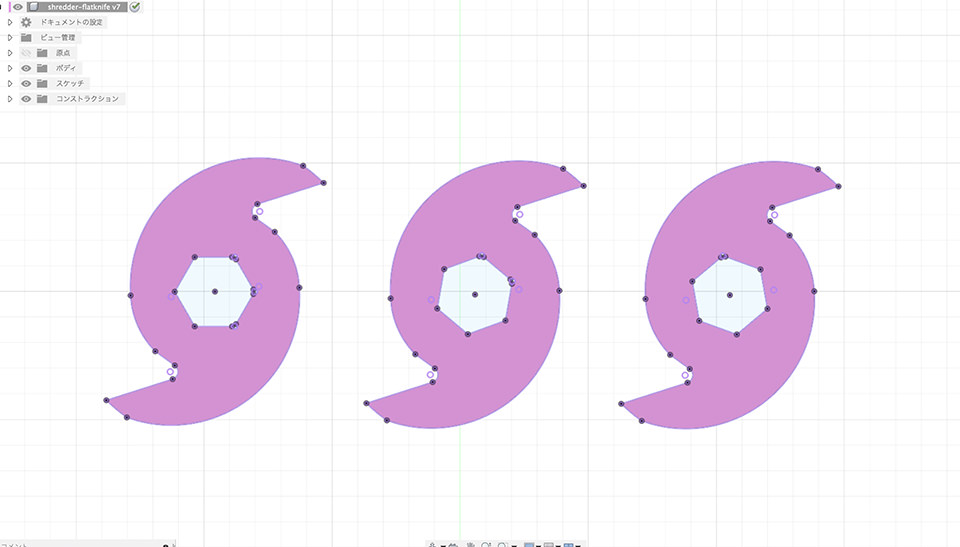
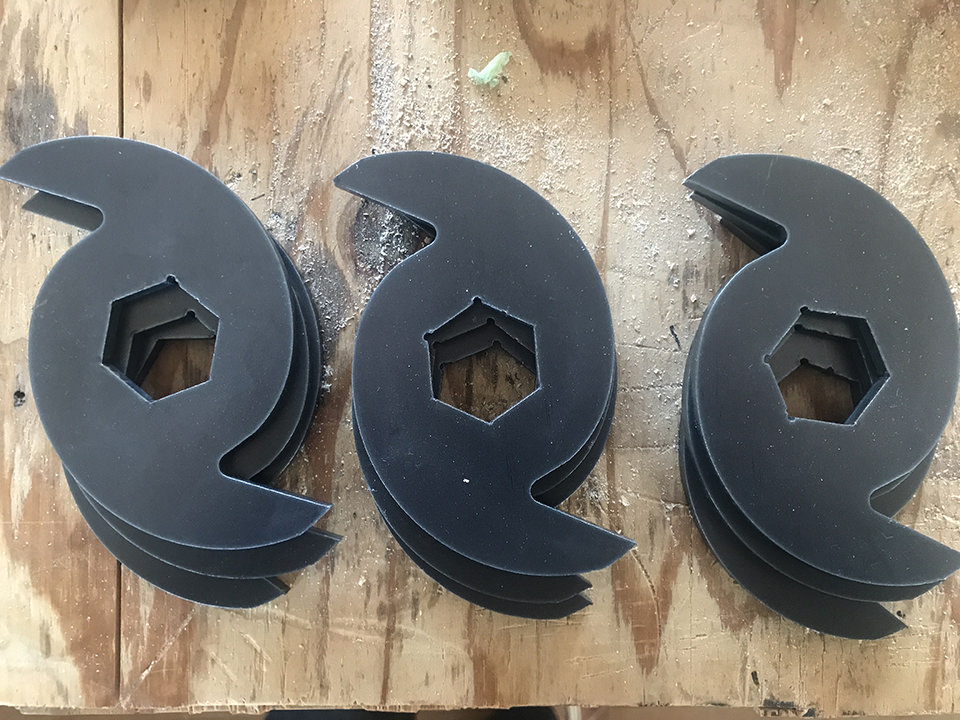
2. パンチングメタル(ふるい)の仕様変更
これは穴をもうちょい大きくした方が破砕後の粒度と効率のバランスが良くなるよ!とのこと。採用したい。
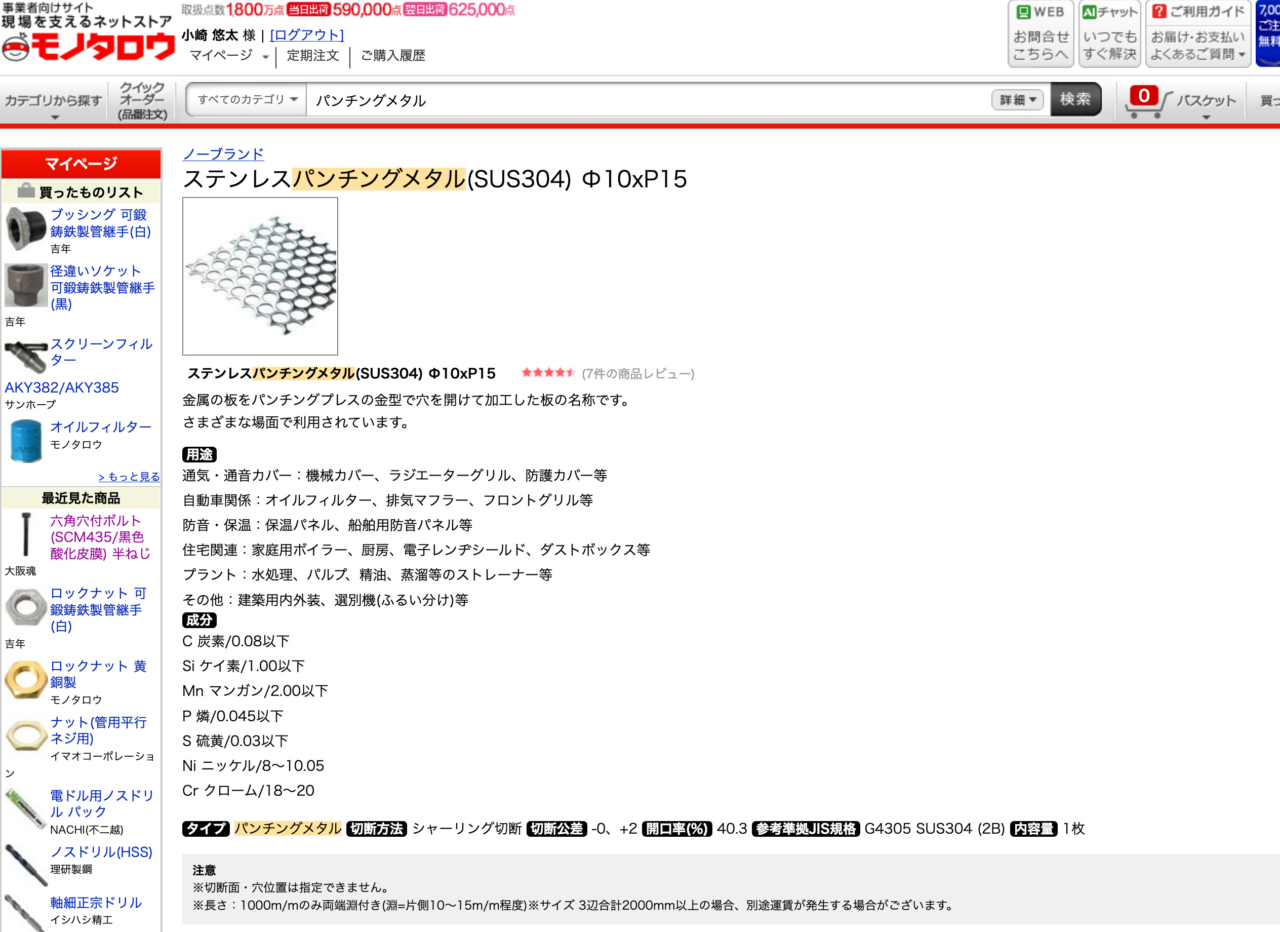
モノタロウで改善案に近いサイズのパンチングメタルを発見(10mm穴が15mmピッチで空いてるもの)。あとから気づいたけど、レーザーカットで発注しても良かった(その方が安いと思う)。
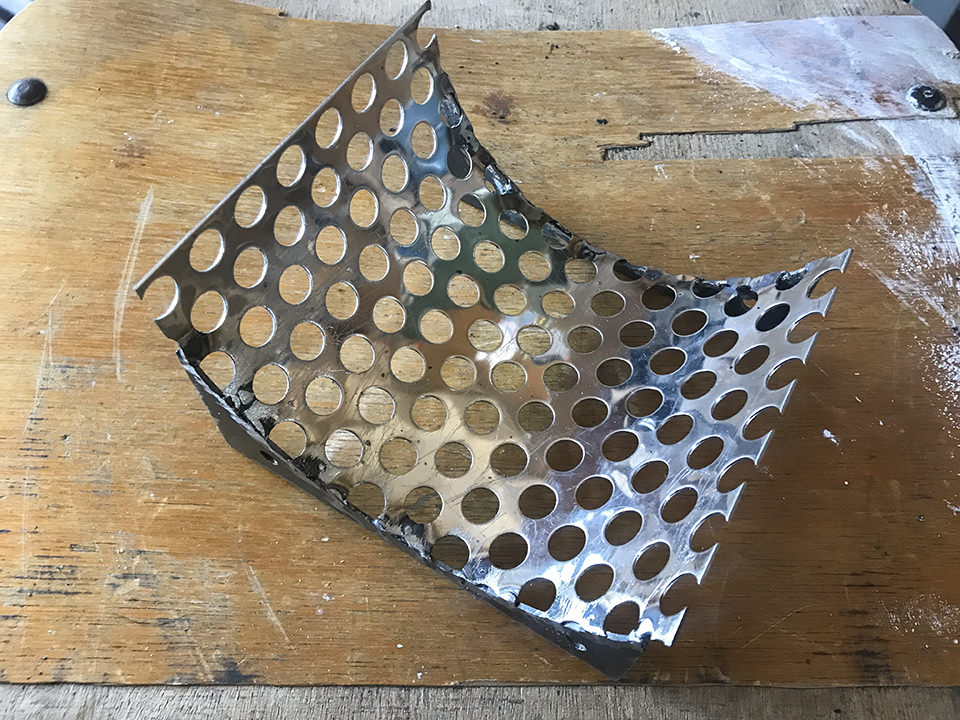
とここで一旦、金属加工の鬼である原先生(おじいさん)に、どんな改善点が考えられるか相談してみる。
するとおじいさんは言うのであった。
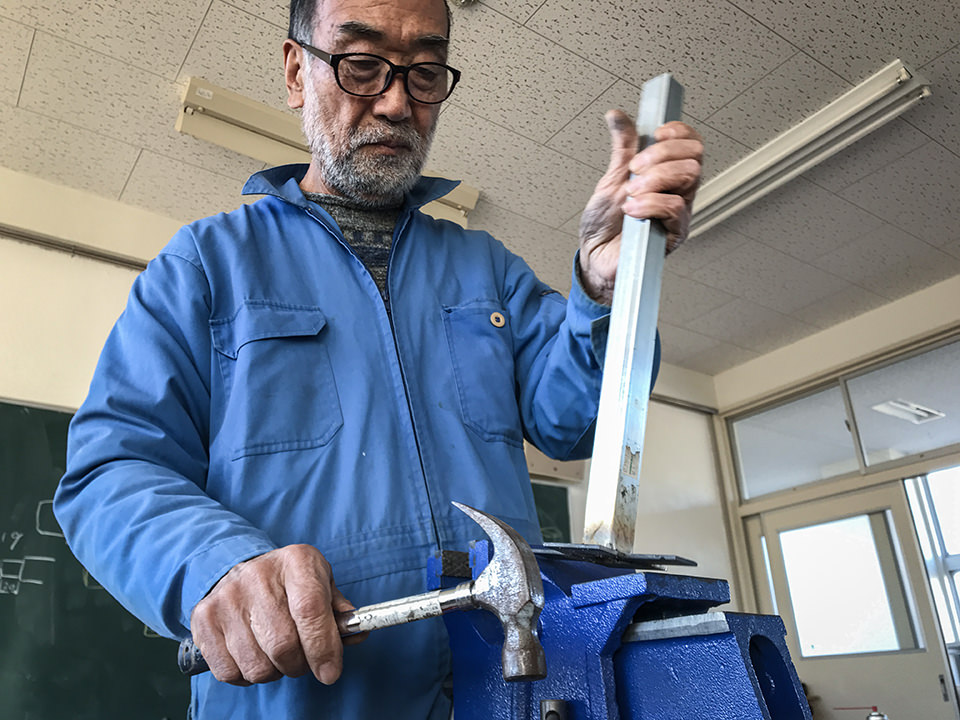
「こりゃお前、クリアランスだよ! こんなんじゃダメだ! 俺はひと目見ただけでわかったね!」
鬼! さすが鬼!
3. クリアランスを変える → 片側0.5mm → 0.25mmに
おじいさんいわく「理屈上クリアランスはゼロでいいんだ。現実的な諸問題で多少クリアランスを取るが、ゼロに近けりゃ近いほどいいだろう」とのこと。
ちなみに、この時点でのラボシュレッダーは、クリアランスが片側0.数ミリ、もう片側がなんと1.5mm(!)あって、実質的には半分の剪断しか起きていない状況。 片側のクリアランスが1.5mm弱もあるために、そこに破砕片が詰まり、クサビのようにブレードナイフを止め、モーターが止まっちゃうのでした。 これまで大してでかいものを砕いていなかったものの、軸を止めるボス(コネクタ部品)を止めるM10ネジは盛大に歪み、分解するのも大作業。
また、公式のバーンジョン2シュレッダーは、クリアランスが0.5mmずつになっている。これは、世の中のステンレス板の規格が、5mm厚の次が6mm厚なので、5mmと6mmの鉄板を使って作ったからだと推測を立てる。
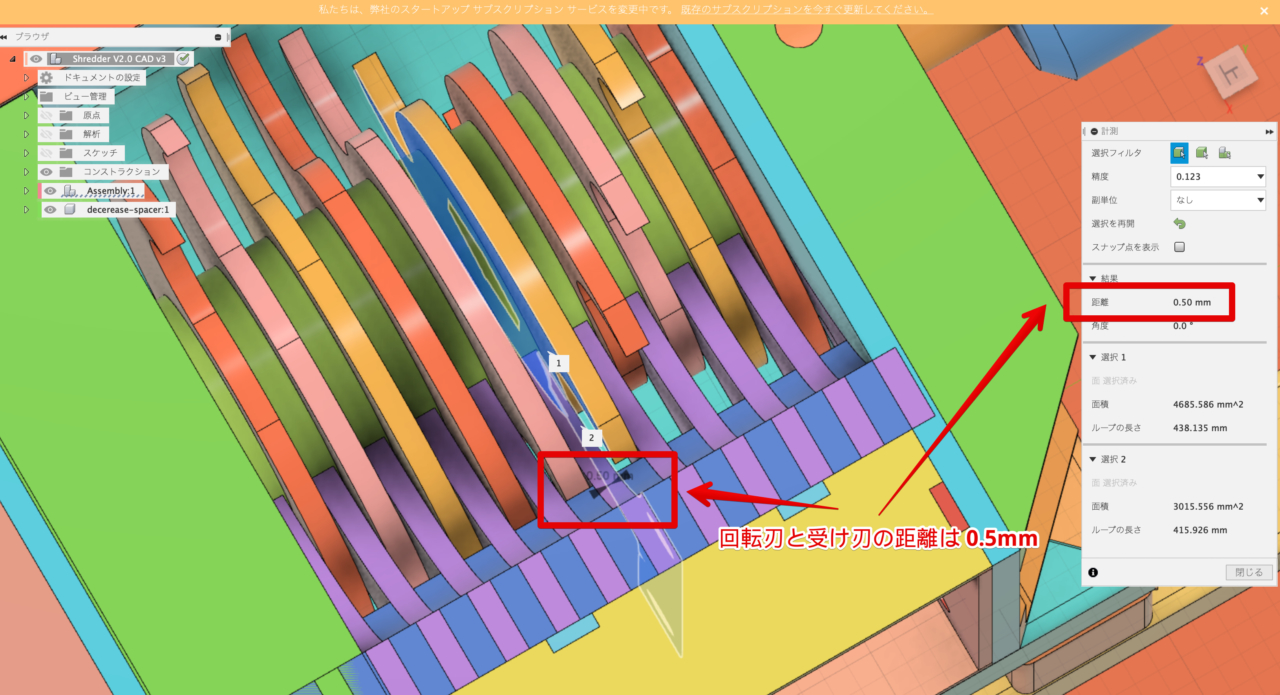
クリアランス0.5mmに意味があるのではなくて、規格品で作ると0.5mmにせざるを得ない、が正しい理解だと思う。
またまたちなみに、ラボシュレッダーはステンレスではなく鉄板で作ってもらった(ステンだと値段が倍高くなる、と言われた)。そうなると鉄板の規格は4.5mmの次が6mmになので、1.5mm空いてしまった、というわけ。
んで、ここからがとても重要なのだけど、レーザーカット加工は安い。研磨加工は高い。
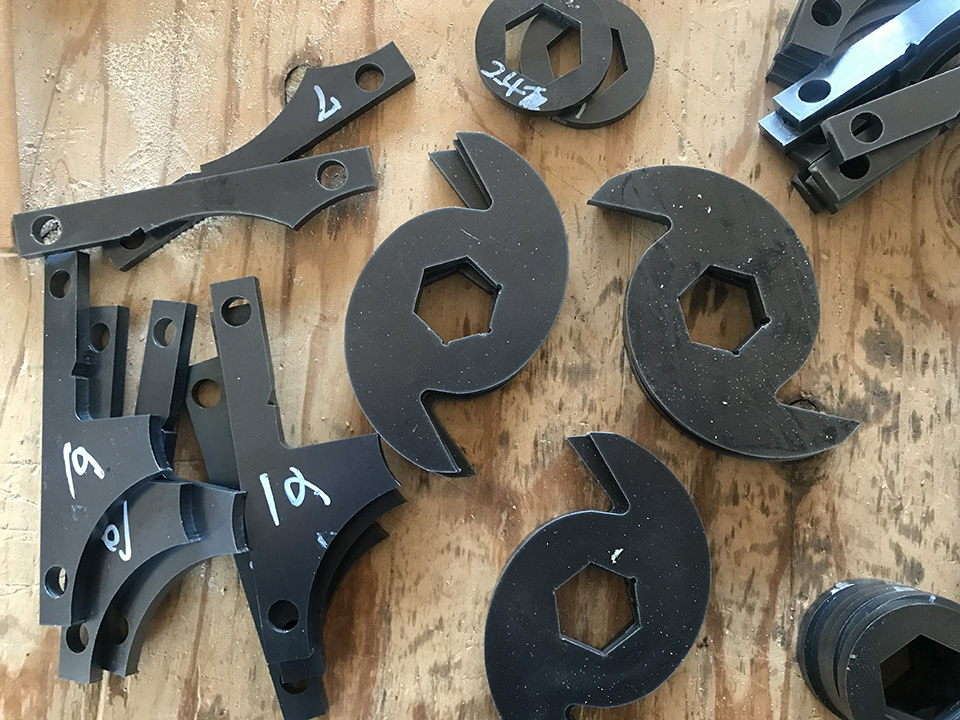
そして世の鉄板は、0.8mm、1.6mm、2.3mm、3.2mm、4.5mm、6mm と厚みが決まっていて、それ以外のものは研磨しないとない。
さらに必要な回転刃の数は15枚前後になるので、発注は常に×15となる。イコールお値段15倍。
ゆえに、市販の厚みのものを組み合わせていかに上手にクリアランスを作り出すかが超重要になるので、1週間くらいずっと考えて結論。
レーザーカット発注は全部6mm鉄板とし、クリアランス分は真鍮やアルミの薄板をハサミで切ってスペーサーを作る。
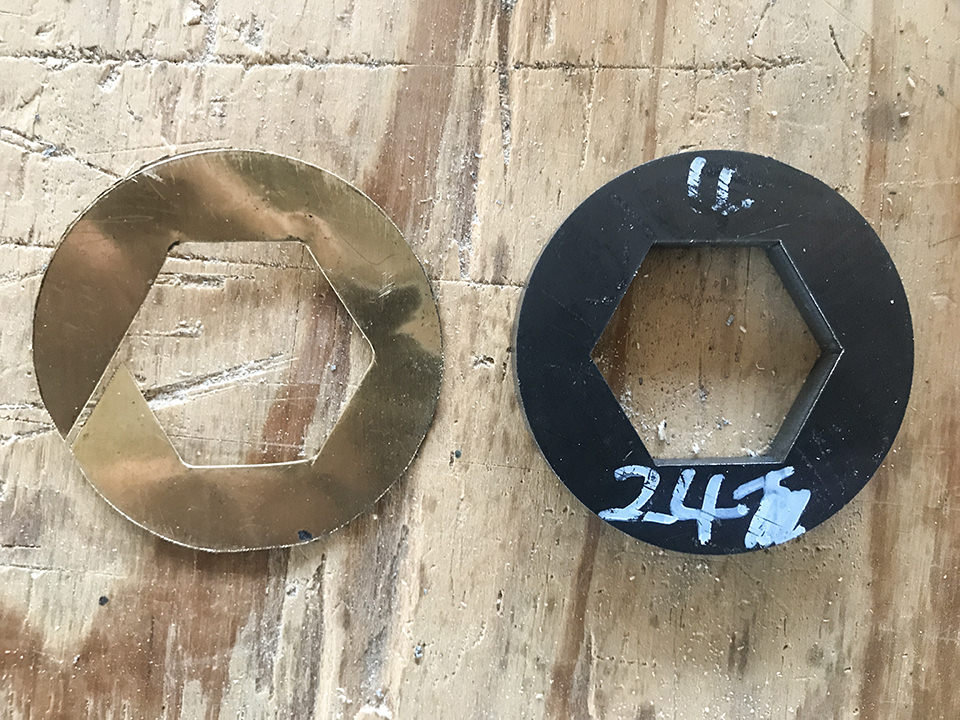
これにより、注文のややこしさが大幅解消(これまでは5mm鉄板と6mm鉄板で似たような部品をたくさん頼む必要があった)。
予算に余裕があれば、スペーサー薄板のカットもレーザーで頼んでも良いかもしれない。自分としては普段、0.8mm鉄板までは手バサミで切ってるので、薄物なら全然手でいけるだろう、と判断。
そして肝心のクリアランス厚をどうするかなのだけど、0.2mmか0.3mmか、どちらかで悩む。ちなみにコピー用紙がおよそ0.1mm。
ここで、バージョン4のプロ版の3Dデータを確認すると、クリアランスが0.25mmになっていたので、ひとまず0.25mmにしてみよう、と私が決定。都合のいいことに、0.25mmの真鍮板の安いものも発見。そして0.25mmにすることを聞いたおじいさんは
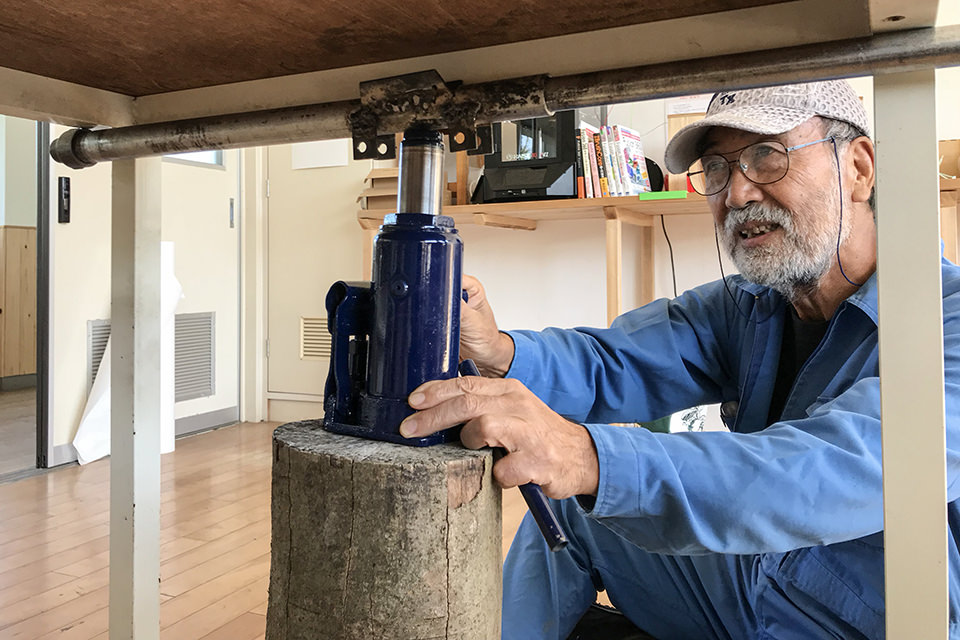
「0.25mmも取るのか? ガバガバじゃねえか!」
やっぱり鬼!
4. 回転刃をなんとか固定する
しばらくラボシュレッダーを見つめ黙っていたおじいさん。やおら鬼が口を開く。
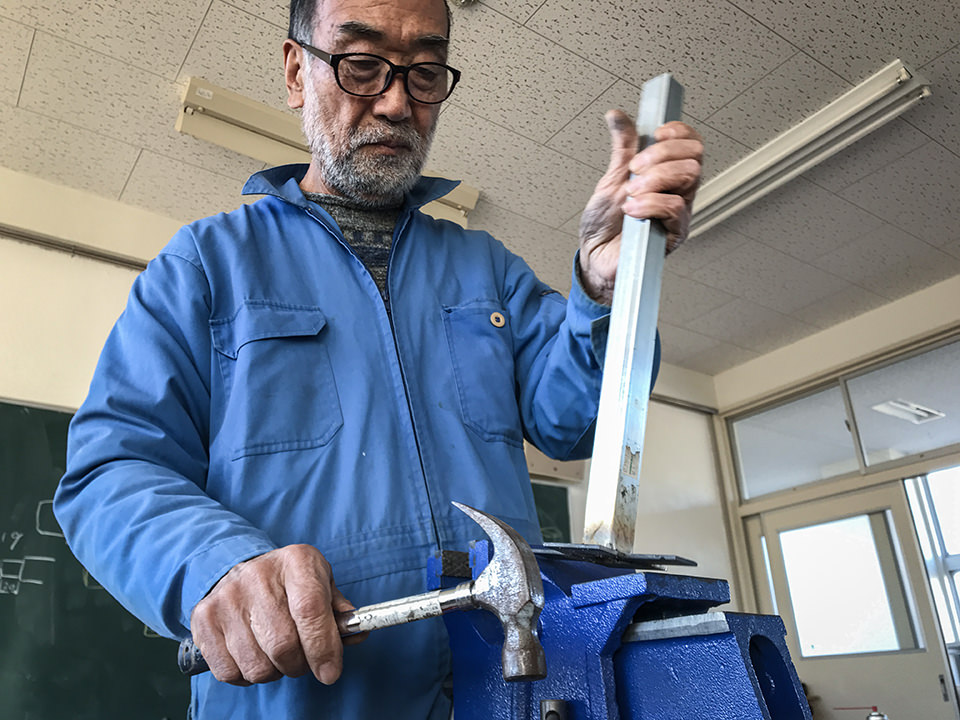
「このシュレッダー(バージョン2)は構造上、回転刃が固定されていないからよお、破砕のストレスがかかった瞬間に、刃が多少逃げるんだろうな。それで隙間が広がって、そこに破砕片が詰まって止まんだよ。…ダメだ!」
その点についてはバージョン4のプロ版で改善されており、やはり公式も同じ結論に達したもよう。
バージョン4では回転刃のシャフトである六角軸の両端にネジを切り、ネジで締め上げて固定していた。
しかし、ダイナミックラボには金属旋盤がないので(絶賛募集中だよ!)、六角棒にネジを切ることができず、これまた考えること1週間。。。
規格品の内径を調べまくって、結論。
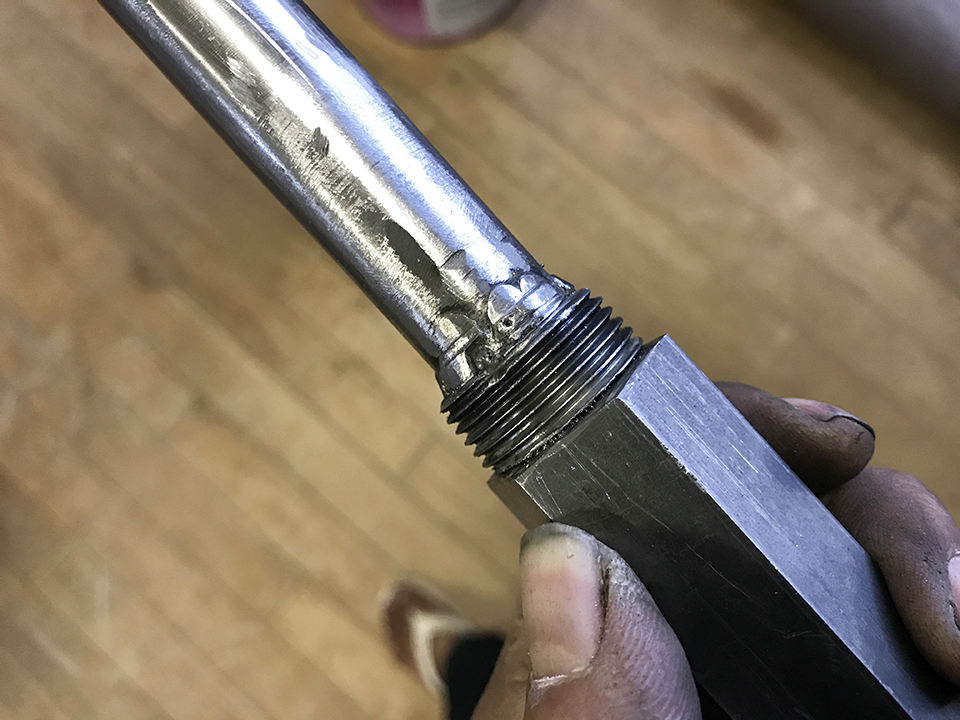
片側は、六角軸の端をぐるりと削って直径21.6mmにし、20A白管ニップルのねじ部をちぎったものをはめて溶接する。もう片側はベアリングのシーラーを直接溶接!
公式の六角軸は、六角の対角27mm、丸部分の直径が20mm。そして20A白管ニップルは内径21.6mmで外径(ねじ頂点)が27mm以下なので、これを使えば、回転刃を通すこともでき、ねじで締め上げることもできる。ナットは20A白管用のソケットを切って使う。すごい調べた!
これにより、刃がほぼ動かなくなったはず。理屈上、受け刃と回転刃との間はクリアランスが0.25mmに保たれたまま滑らかに回転するはず!
たぶん…!
必要なものを発注する
六角棒を削ってネジ化したので、六角部分の長さが減り、使える刃の枚数が減る。よって、全部で回転刃を12枚とし、受け刃2種、六角スペーサーもこれに準じて、12枚ずつ発注した。真鍮スペーサーは逆に24枚くらいずつ必要になるはず。
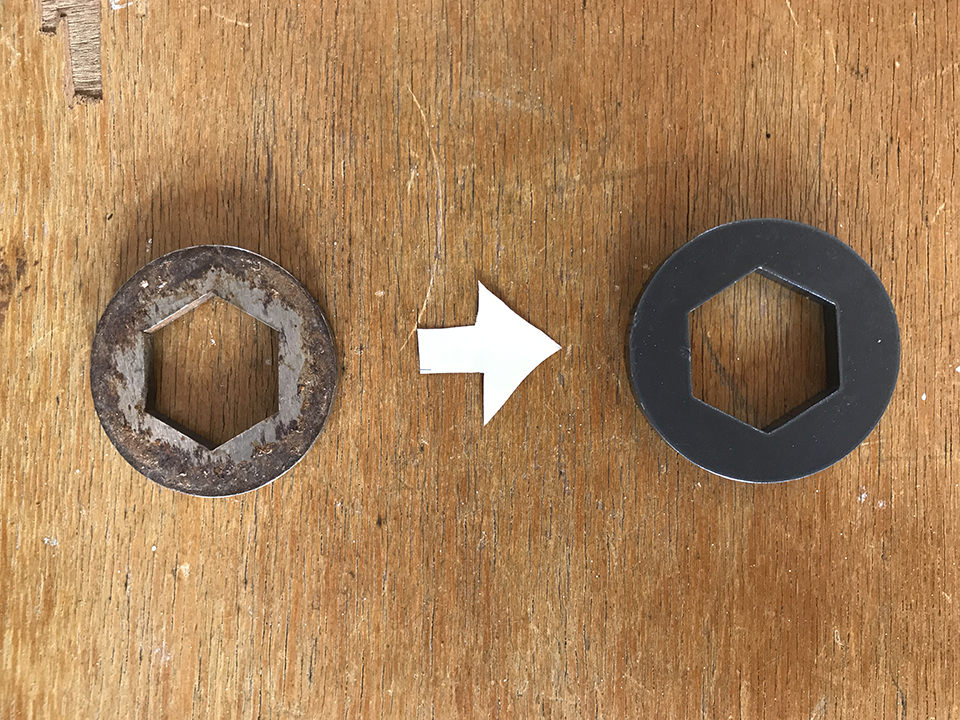
じきにレーザーカット発注品も届く。届いてびっくり、最初のラボシュレッダーの鉄板と厚みが0.2mm〜0.3mm近く違う。(最初のが0.56mm前後、新しいのが5.85前後)
調べてみると、6mmの圧延鉄板の公差はなんと±0.5mmもあるのであった。(だったら、うまく組み合わせればスペーサーいらないじゃん!)
いよいよ製作開始!
人生で一番真鍮板を切った日。
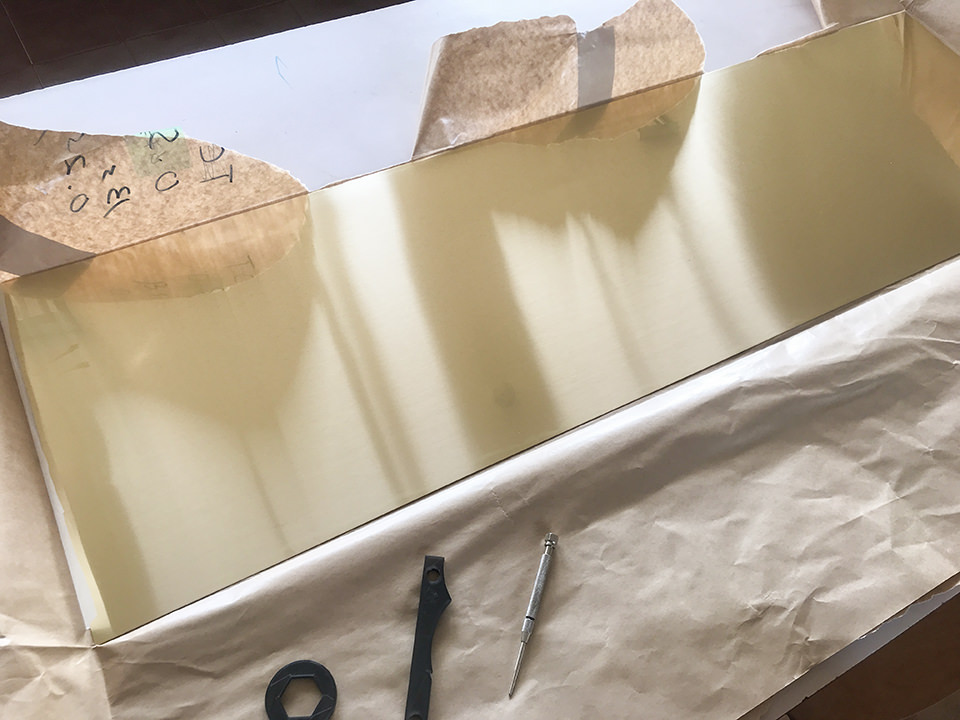
真鍮板が届いた! 綺麗だな! 五円玉を量産しよう
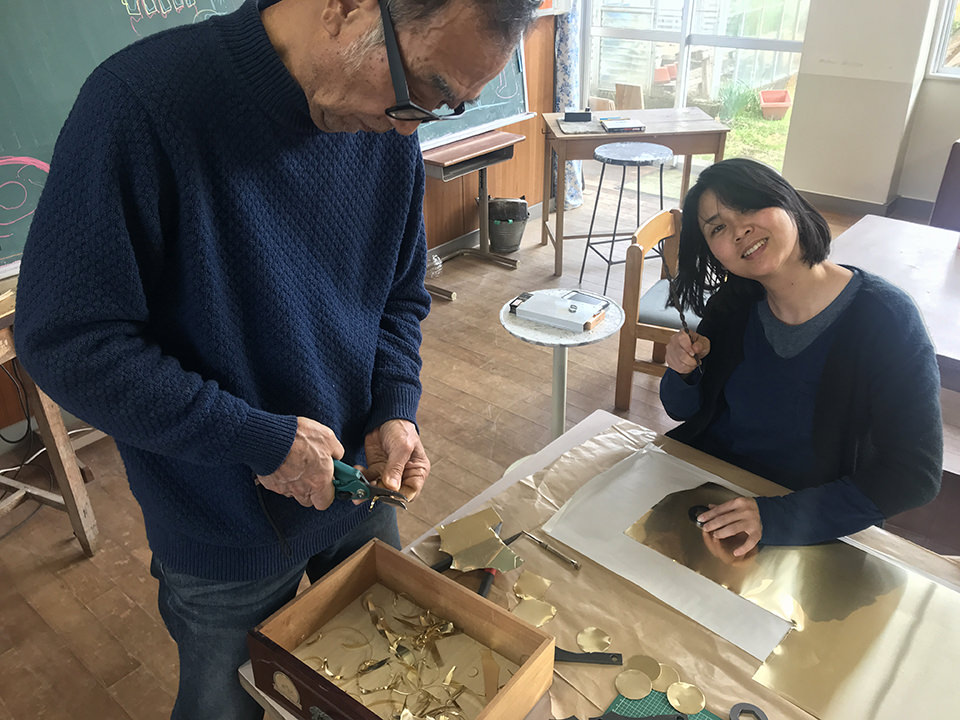
というわけで奥さんにも手伝ってもらって、ひたすらケガキで真鍮に線を引き、金切バサミでスペーサーを切る。
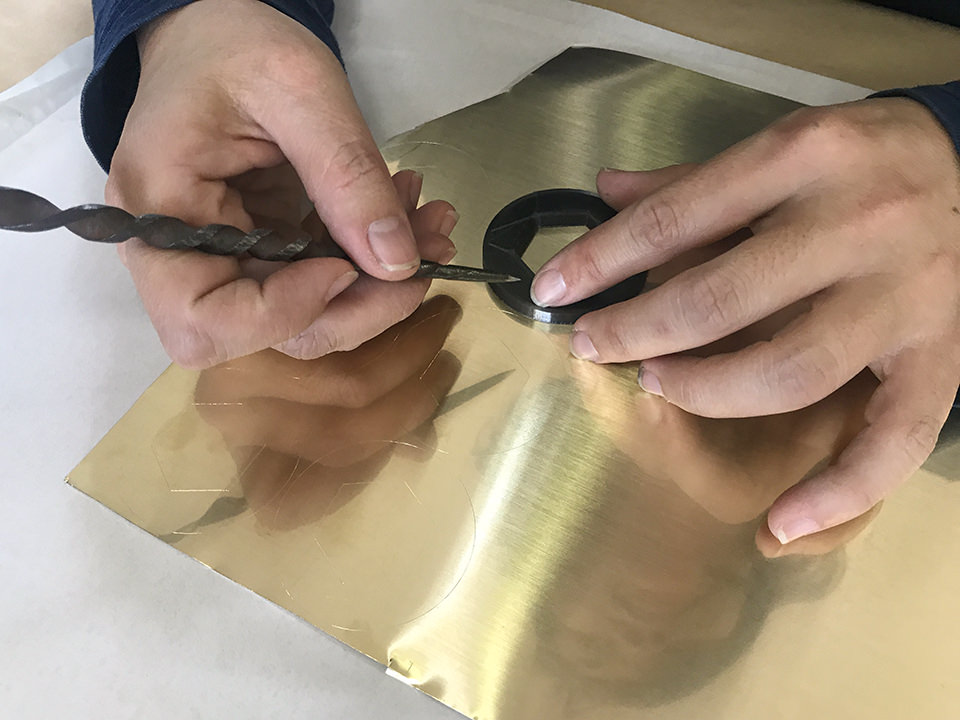
すると鬼が、曲線を切りやすいようにハサミを叩いて曲げてきた。やはり鬼。
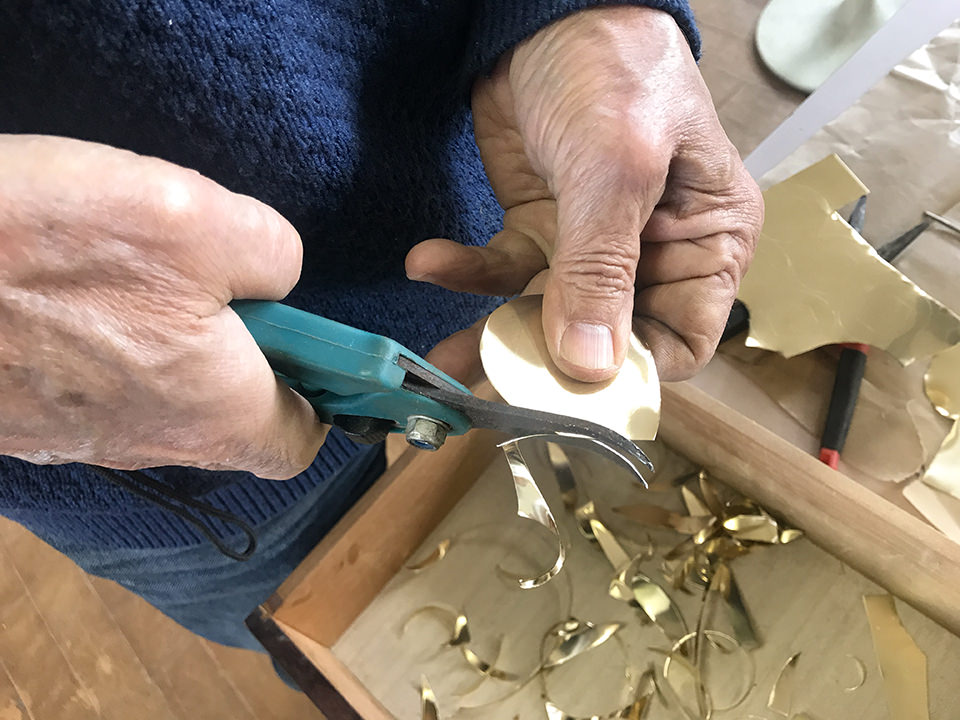
六角の穴部分は、潔く切り込みを入れて安直に切った。これで問題なし。
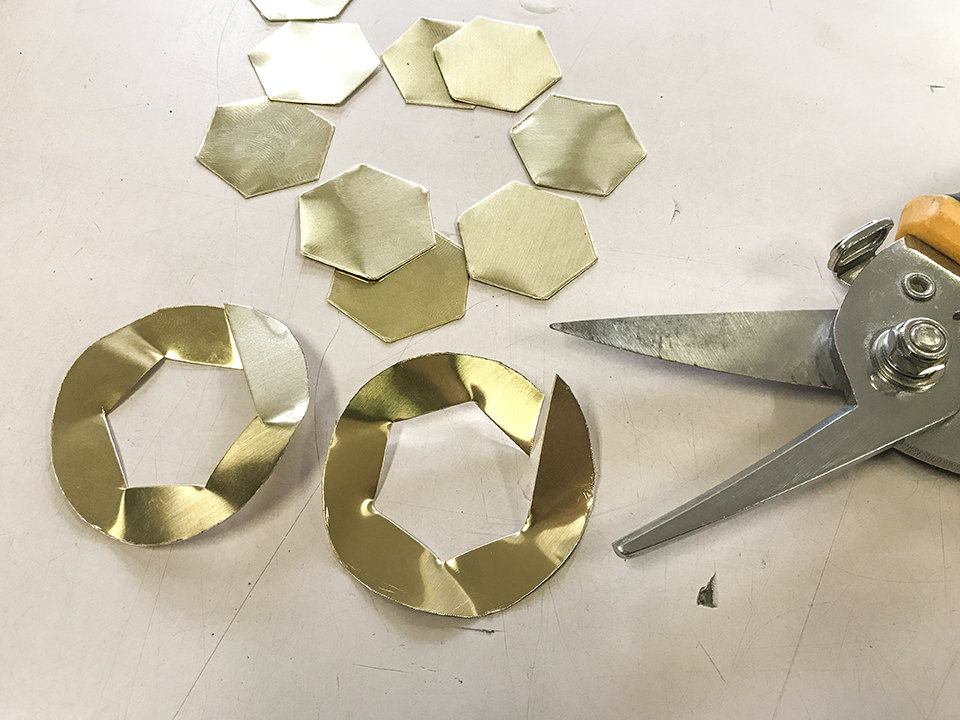
はじめは「こりゃ時間かかるかも、、」と思ってたけど、やってみたら1時間以下で全部終了。簡単であった。
その後、木槌で真鍮板を叩き、ダレやカエリを直す。鬼いわく、こういうもんは叩き伸ばす向きによって全然変わるから、考えながら叩くんだ、とのこと。
六角棒を改造して締め込み仕様にする
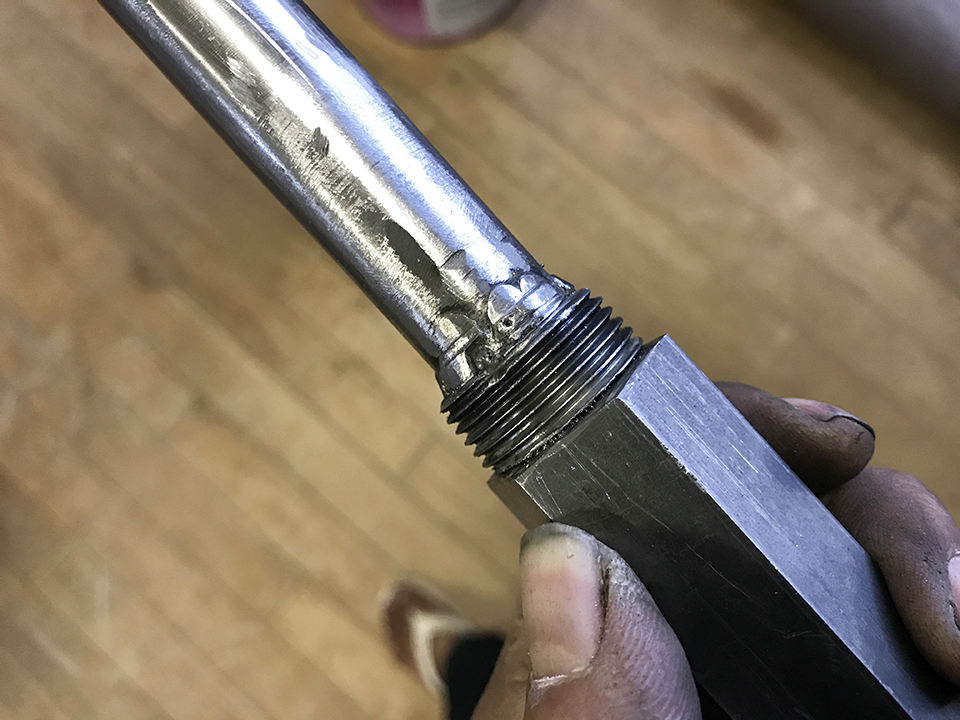
20mm丸棒軸に、白管ニップルを切ったものを溶接。
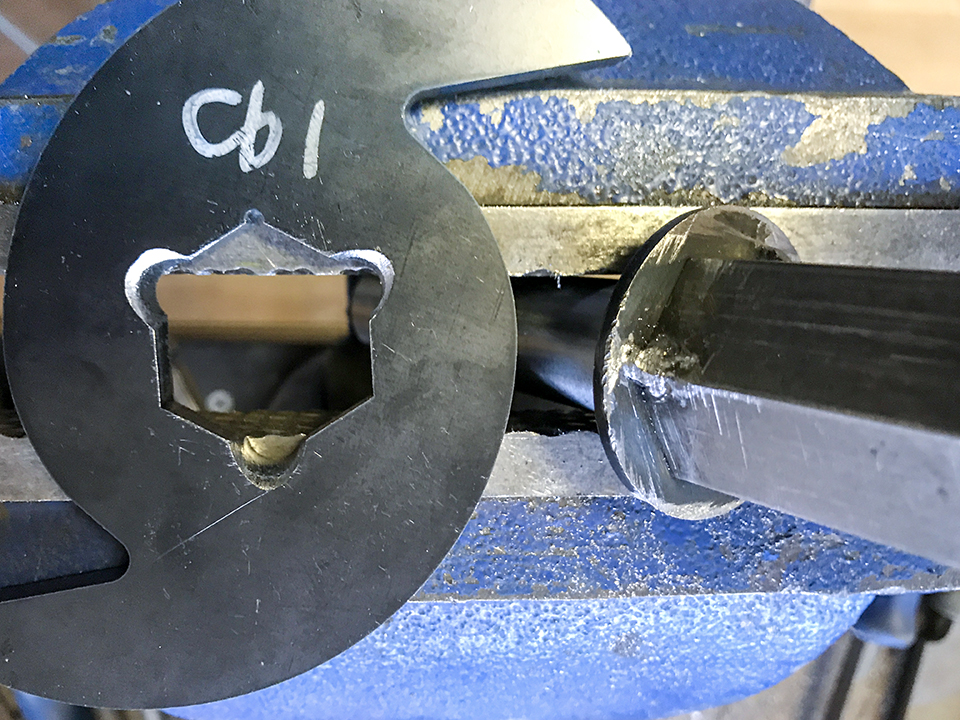
反対側はシール部品を溶接する。ついでに六角刃を一枚だけ、溶接跡を逃すように削る。
とうとうシュレッダー改の組み上げ!
考え、調整しながらおじいさんと組み上げる。
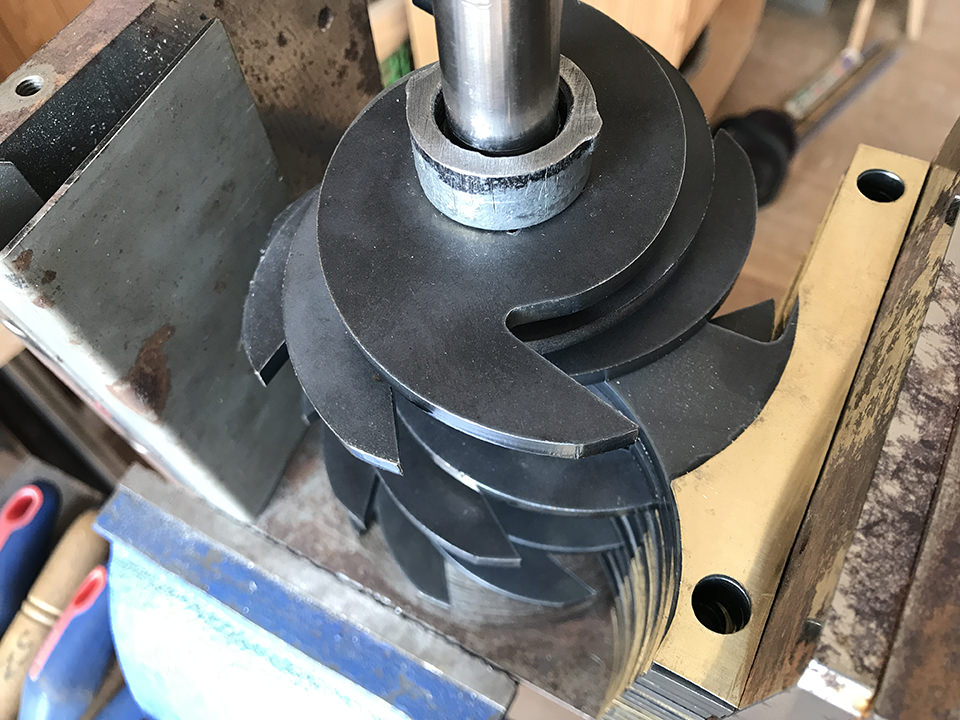
鬼いわく
「とにかく一つ目の刃と受け刃の関係性がしっかり出ているか? そこがきちんと合っていれば理論上、最後まで0.25mmのクリアランスは維持されるはずだからよお」とのことなので、ここの確認のために組んではバラし、組んではバラしを5、6回繰り返す。
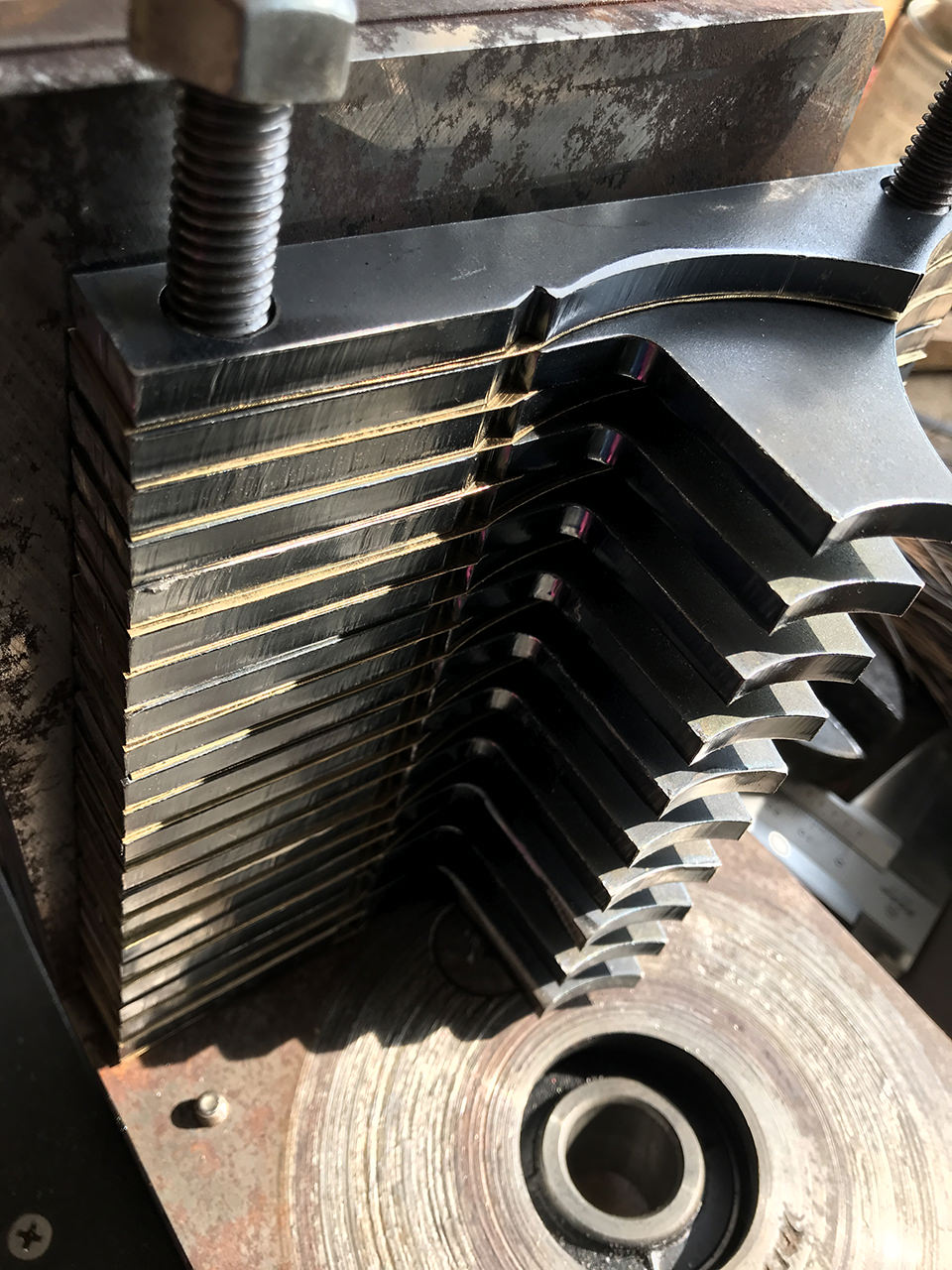
最終的には受け刃の方のスペーサーとして、ワッシャーを2枚削って入れ、それでももう一声足りないので、鬼の指示に従ってなんと厚紙を入れた!
厚紙でいいのかー! いいらしい。知らなかった。
そして、電源を入れると、、、
おおおおおおお!!!!!
当たり前なんだけどスムースに回ると嬉しい。初期は多少真鍮板の干渉があったものの、刃を回すうちにスムースに。
ふるいとホッパーをつけて、いざ破砕!
極上の破砕体験をあなたに。
いや、もうね。今までの破砕がなんだったのか?というくらい性能が違う。
全然詰まらない。ホッパーに山盛りプラゴミを入れたときはモーターのパワーが足りなくなって一瞬噛むことがあるけど、山盛り入れなければ全然大丈夫。
うーん、大幅改善!
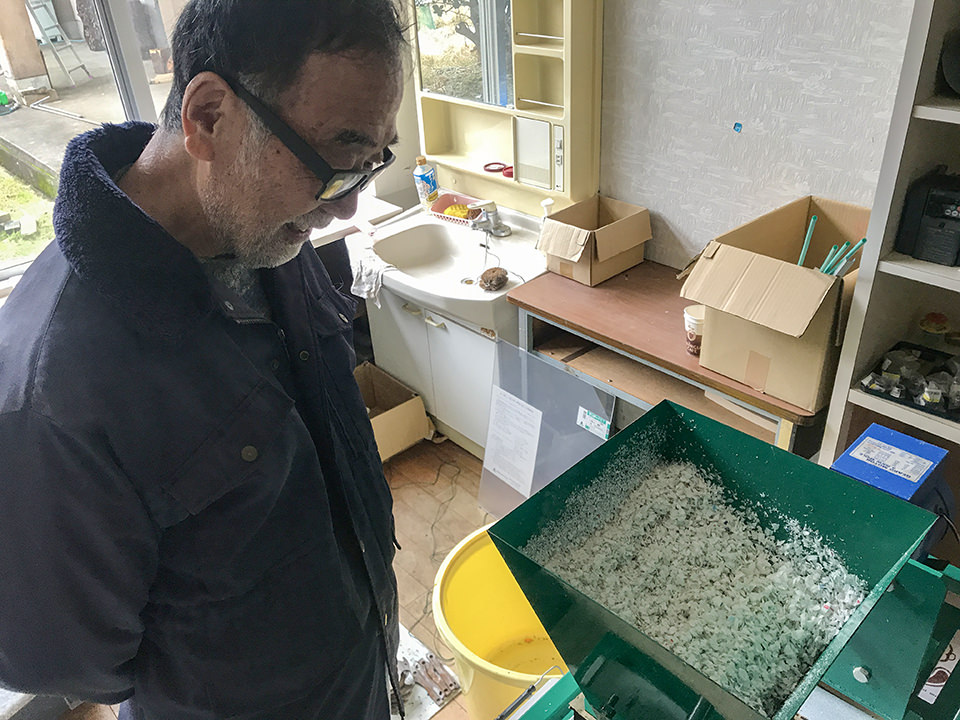
しかし、まだまだ改良(と書いてドキドキと読む)は止まらない・・・!
イ. 固定刃の押さえ方式を変更
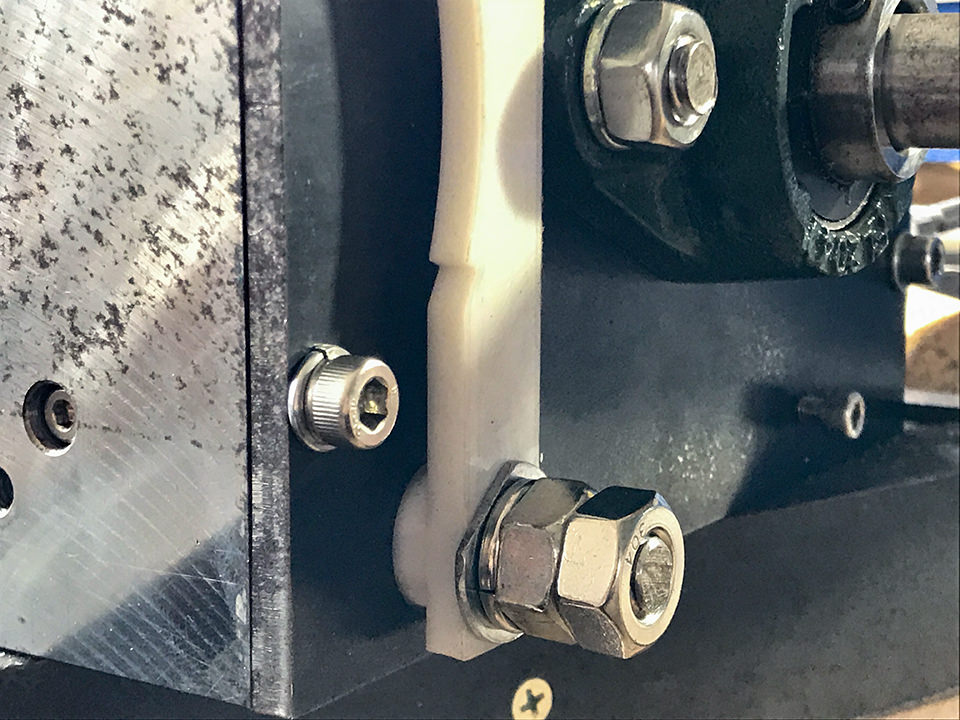
厚紙で押さえるのはなんなのと、そもそもガワの箱は箱で精度がキチッと決まり、固定刃は固定刃で精度が決まっていないと(要は、互いに独立していないと)、機械設計上おかしいので、固定刃の押さえ方法を考案した第一弾。
元の軸穴を16mmまで広げ、それに合う3Dプリント部品で押さえる。
(箱の中に入れるつもりで作ったものの、外から押した方が可能性が広がるので、最終的に外からくっつけた)
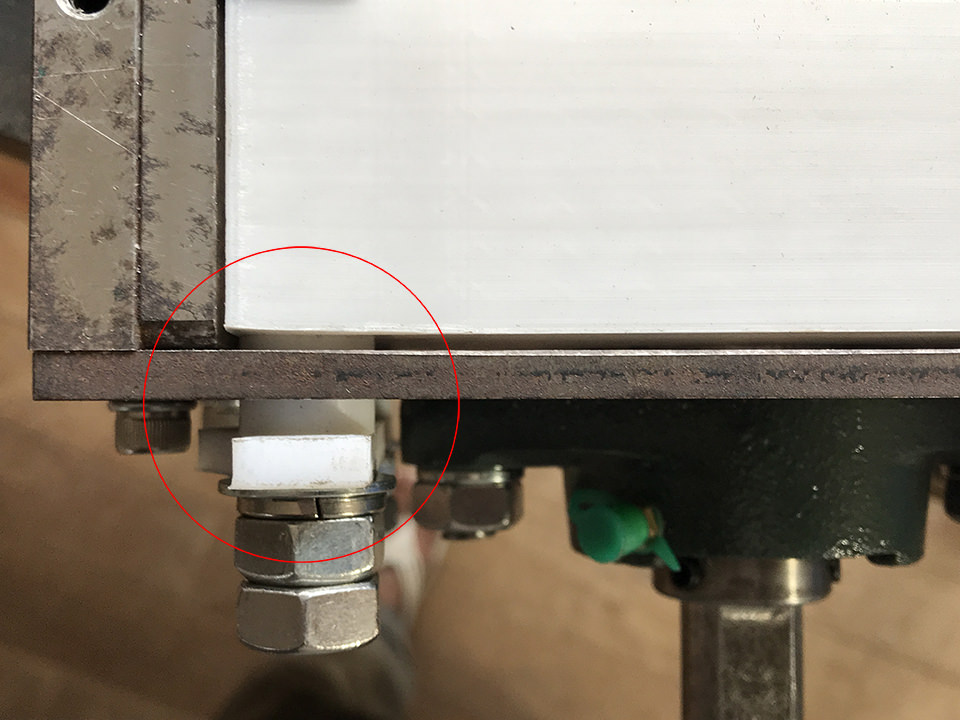
ただしこのやり方だと固定刃の位置出しが怪しくなるので、のちに押しネジ方式に変更。
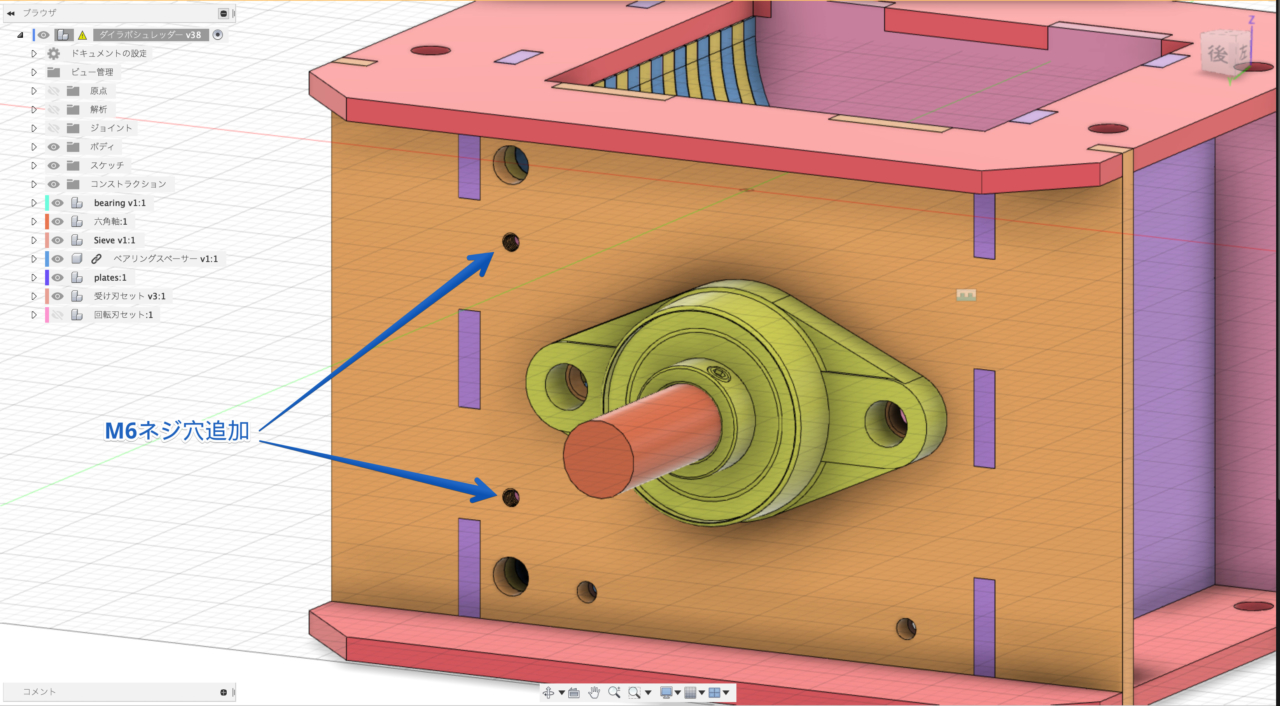
ロ. ベアリングの位置だしにレーザーでケガキ線をマーキング
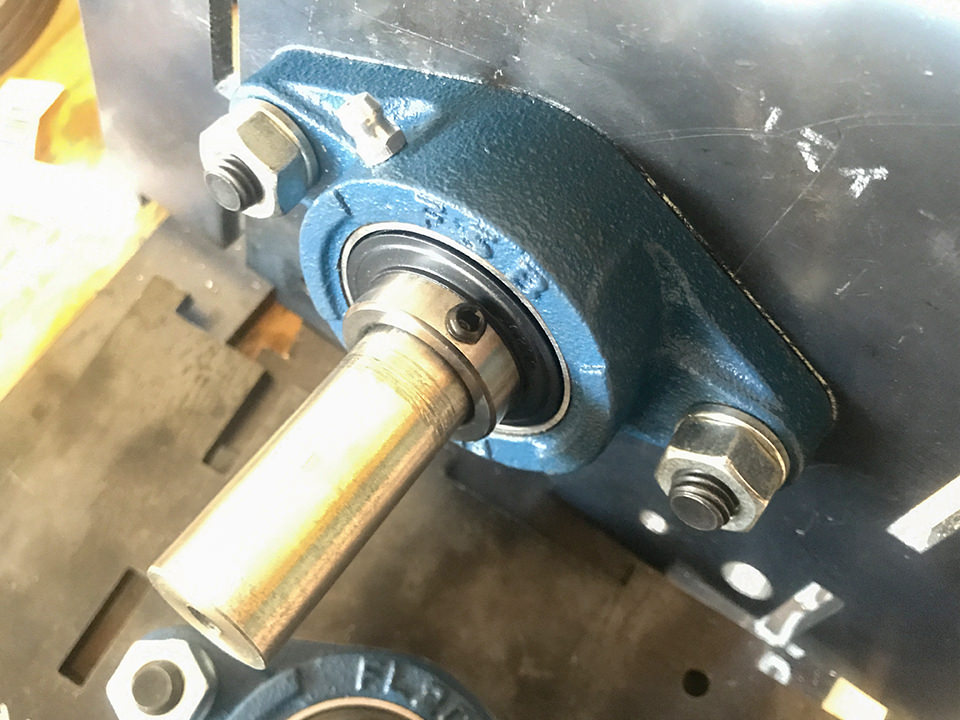
レーザーカットの精度が怪しいことがあったので、レーザーカット時にベアリングのケガキマーキングも発注。そのケガキ線に合わせた。
これならかなり柔軟に精度出しができる。
ハ. そもそもこの破砕負荷は、果たしてモーターに対して適切なのか?
ホッパーに山盛りプラゴミを入れる実験を繰り返して、だんだんと噛んで止まるときの理由の目星がついてきた。
ひとつめは、回転刃螺旋送り問題。
回転刃を規則正しく並べると螺旋に近い形状になるので、材料を端へ端へと送ってしまう。すると、一番端の刃一枚に材料と負担が集中して、たぶんそこが噛む
これは、刃の並びを不規則に散らすことで解決できた。ただし材料が跳ねやすくなる気はする(順次刃が破砕してくれる確率が減る・・・のか?)
ふたつめは、山盛り投入窮鼠猫を噛む問題。これは材料を山盛り入れるとおそらく
・「量が少ないときにはホップして(跳ねて)逃げられてた材料が逃げられなくなる」
ことと、
・「その結果、行きがかり上切らざるを得ない状況」
とが複合するからなのだろう、と推測をつける。
この山盛り問題はプラゴミの量をたくさん入れる限り避けられない境遇なので、このこと自体はどうしようもないが
・ホッパーに入る量の調整
と、
・行きがかり上切らざるを得ないときに、材料にかかる力
は変えることができそう。
ホッパーは変えればいいだけなのでひとまず置いといて、問題は材料にかかる力について。
単純にはモーターの規模をより大きくすればいいのだけど、日本ではご家庭の100V用モーターはほぼ750W(1馬力)までしか流通していないらしく(※テンダーヤフオク調べ)、今回使っているモーターをMAXとして捉えた方が現実的(汎用的)だと思う。
次に、現在の回転刃の枚数が12枚。これをつぶさに見ていくと、10枚目以降は1枚目と同じタイミングで材料に当たることになる。
ということはつまり、10〜12枚目までの3枚があたるタイミング(12分の3=機械が回っている時間の4分の1)は、モーターの力が必ず二枚の刃で二分される、ということ=パワー1/2!。
ゆえに、刃を9枚にするだけで
常にモーターの1分の1の力が材料に当たることになる&レーザーカットする材料が大幅に減る=製造原価圧縮&軽量化!!!
これは・・・やってみる価値がありそうだッ・・・・!
3Dプリンタを使って、刃の枚数を減らしたバージョンを実験
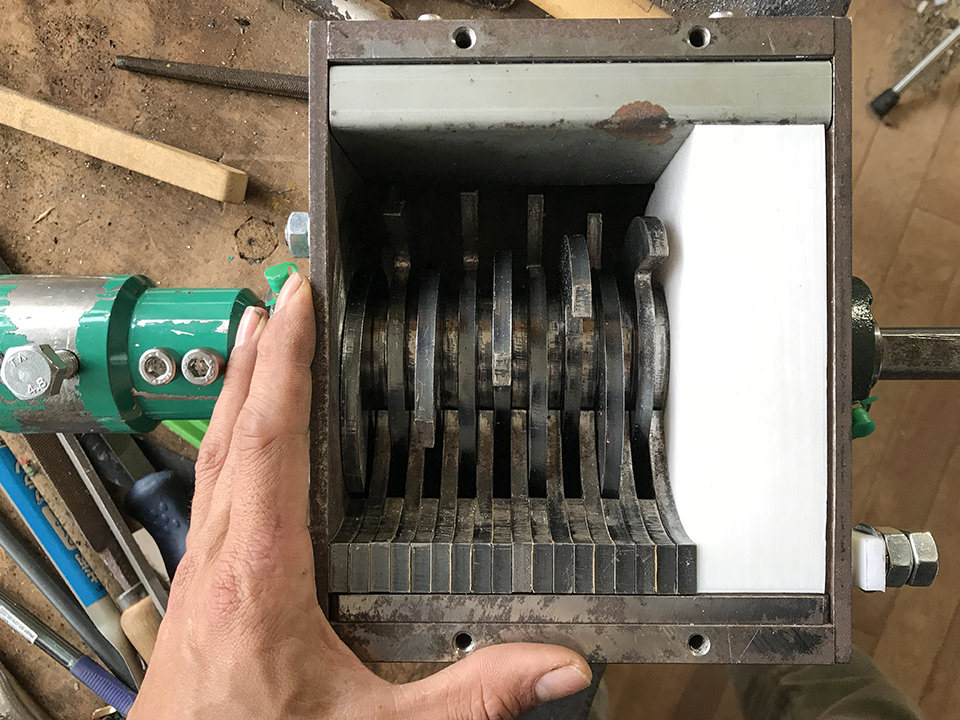
サクッと、刃3枚分のスペーサーを作る。ピタピタなので、破砕片も巻き込まない。
ごっつくて見た目は悪いが性能は十分。 こういう複雑な形状のスペーサーを精度を保持しつつ作れるのが3Dプリントのすごいところ。
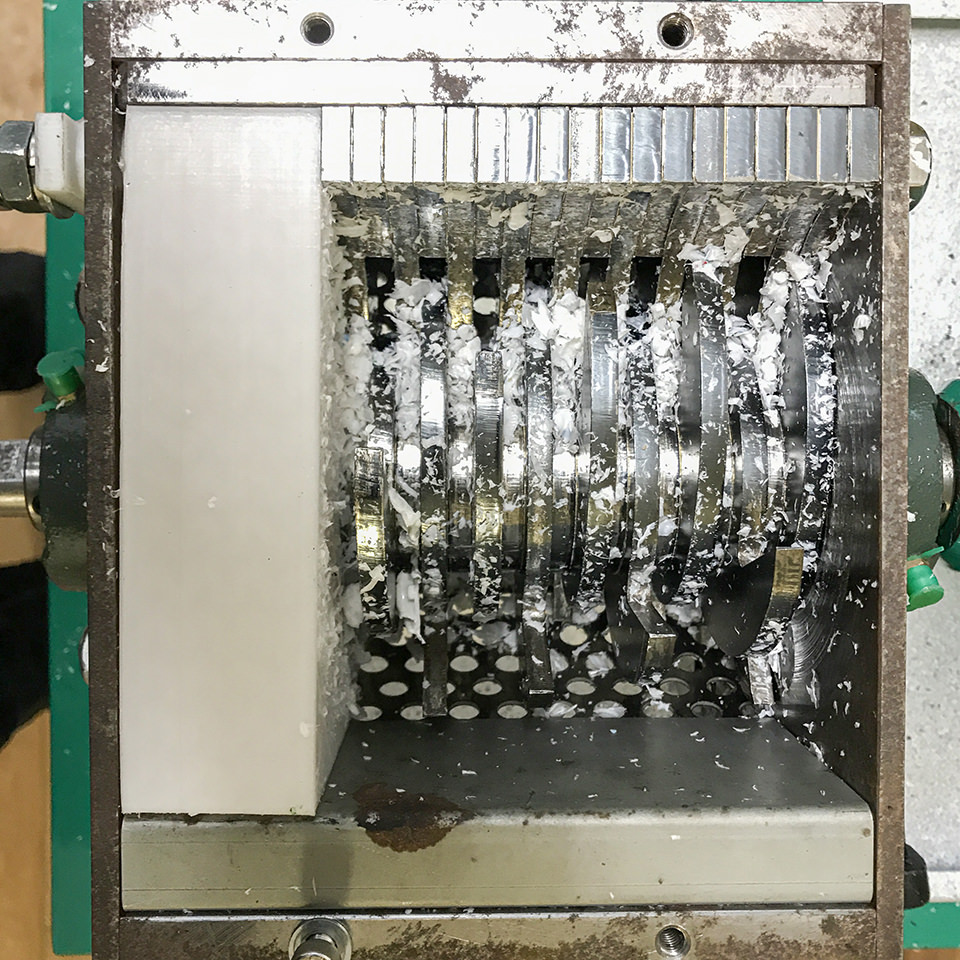
ついでにホッパーも直筒式に変更。側面を透明にして進捗を見えるようにした(お客さんはみんな中を覗きたがるが、中に指を突っ込むと指がなくなるので、透明化して見えやすくなることは安全上の理由も兼ねている)
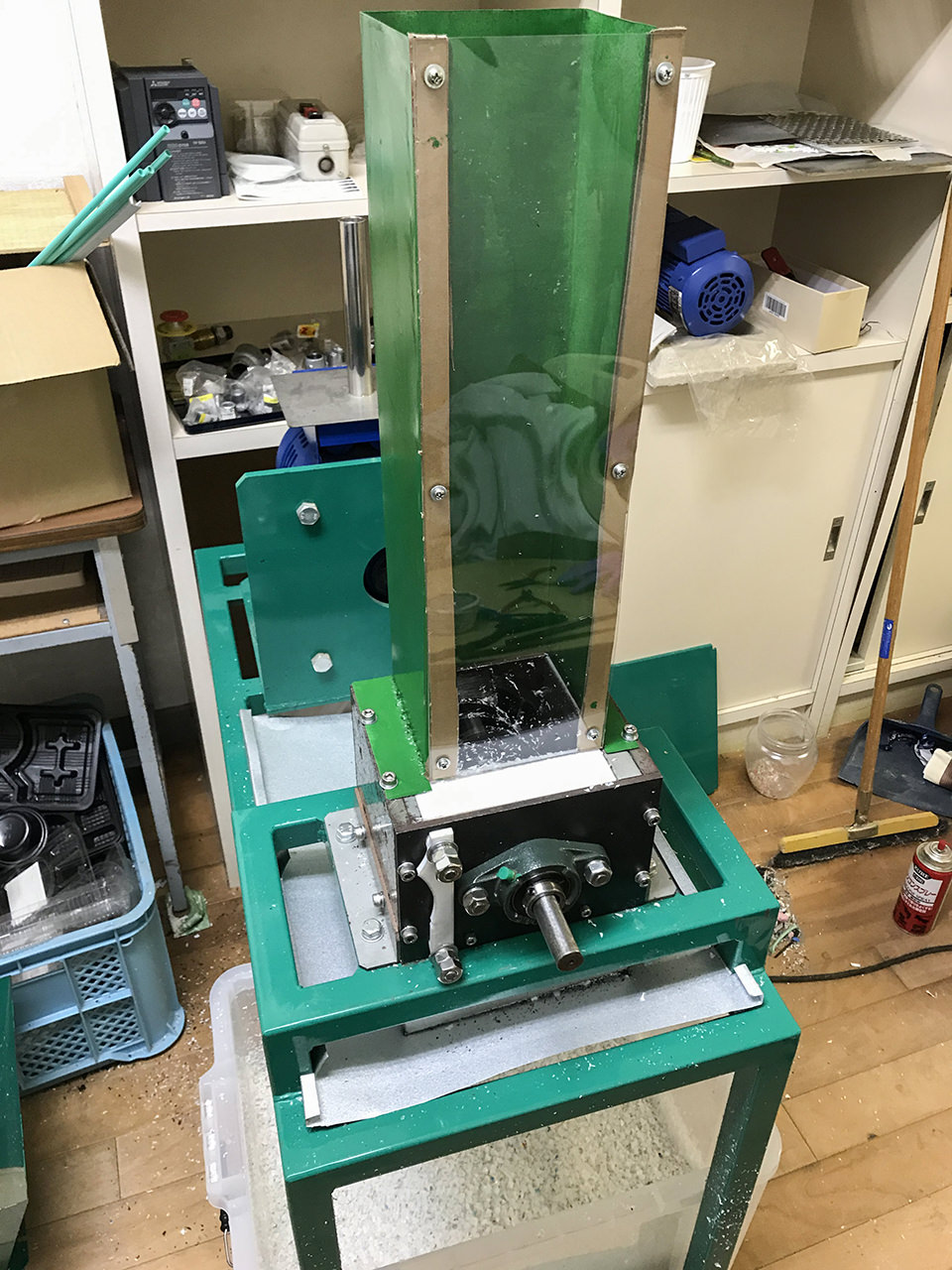
いやー、完璧だ・・・。
ホッパーに入る量が減ったこともあるけど、モーターが噛んで止まることがなくなった。そして速い。
山盛りペットボトルキャップの破砕で、粒度7mmくらいまで、5分かからないくらい。
理屈上、刃を減らせば破砕できる量は減っていることになるけど、そもそも破砕できなくてモーターが止まったら意味ない(その時間は作業の完全な停止+復旧作業を意味する)ので、トータルで見ると効率化されている、と言ってよいであろう!
もろもろ総括して改良したダイナミックラボシュレッダー(for Japan model)
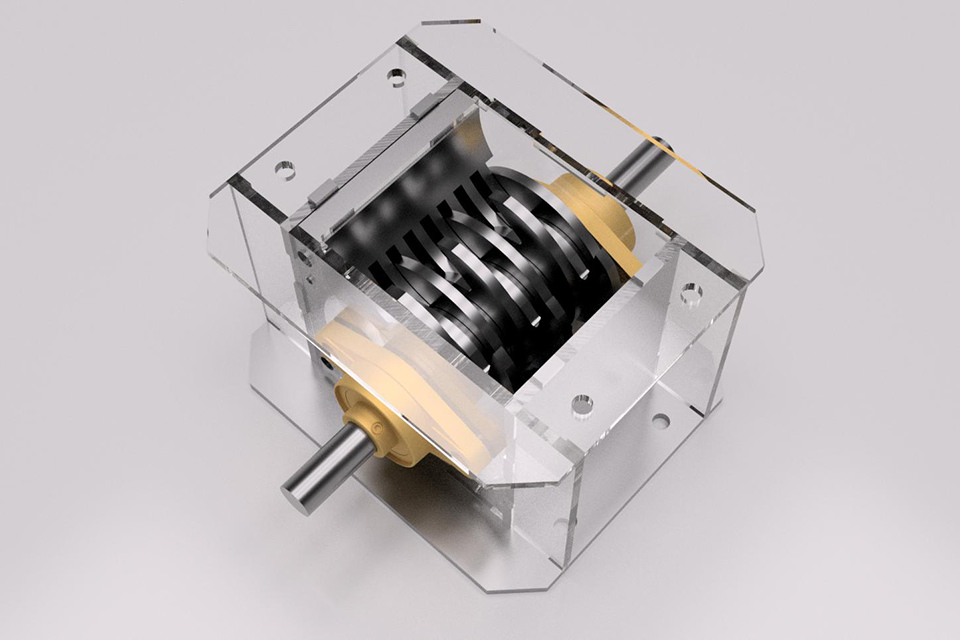
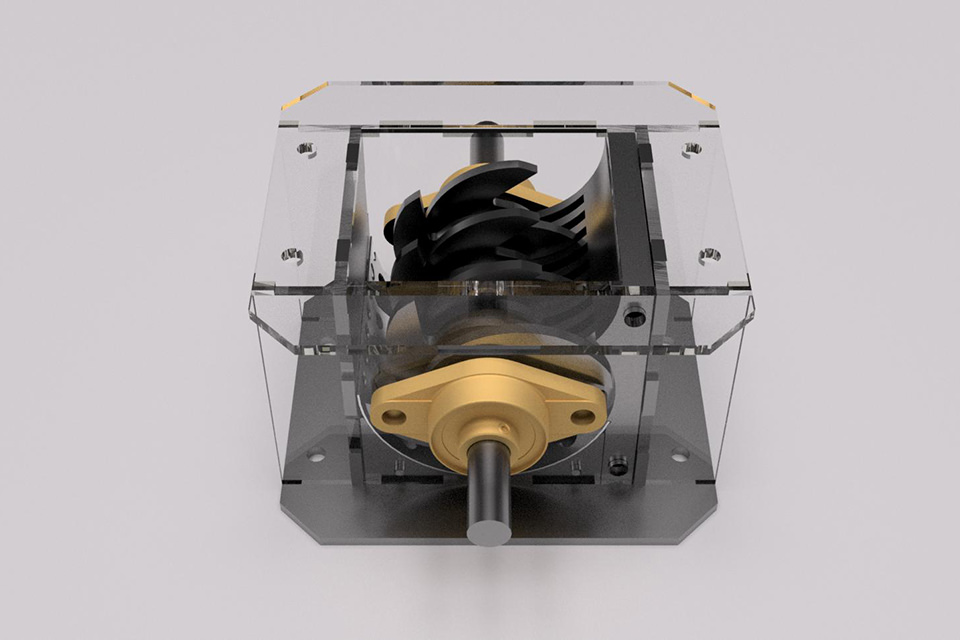
以上を踏まえて、そもそもガワから再設計しました! 頑張った!
(またまた時を同じくして、シンプル版のver3.1が発表されないままなぜか販売されていたので、その写真を見つつ取り入れました)
主な改良点
- 部品の大部分が6mm鉄板で済むようになった(発注がシンプルになった)
- 部品点数が大幅に減って、安くなった
- 部品点数削減に伴い、軽量化された
- 日本の100V電源で扱いやすいように最適化した
- 元のV2の抱えていた不具合が解消された(刃形状、刃固定されてない問題、クリアランスの幅広さ、規格上ステンレスじゃないと作れない問題)
デメリット(あんまりないけど)
- 時間当たりの刃に当たる材料の量が減った
- 組み立てに0.1mm基準くらいの精度が必要
いやー、やってよかった! ちなみにこれは鹿児島県南さつま市の助成金事業として、10万円の給付をいただいて取り組んでおります。ありがとう南さつま市!
諸経費(既存のprecious plastic shredderを改造した時)
- 6mm鉄板のレーザーカットで部品代 / 35000円〜40000円くらい。
- その送料 / 1500円くらい
- 20A白管ニップル / 100円
- 真鍮板 t=0.25mm / 3000円くらい
- その他3Dプリント、軸加工など。
今回の製作はたくさん試作やらテストやらしているのでもっとかかったけど、既存のシュレッダー改良であればそこそこの値段でまとめられるはず。
というわけで、追って、世界の precious plastic コミュニティにもご報告と共有をするつもり。オープンソースに加わって、自分で改良してフィードバックするのが初めてなので、嬉しい。
あと色々考えたけど、これは手回しか自転車動力かにした方が意味があると思う。ひとつはモーター合わせ問題(ヤフオクでモーターを探して、ちょうどいい接続部品を都度旋盤で作る必要がある)があるし、
もうひとつは人の業によって環境に流出しているプラスティックを人の手を通して再度作り替えていくことに意味があるんじゃなかろうか、と思った。
長くなったので一旦ここまで。お疲れさん!
コメント
コメント一覧 (4件)
感動しました!お疲れさん!
あざっす!がんばりました!
[…] 記事:安い!簡単!効率いい! precious plastic シュレッダーを大幅改良しました より […]
めっちゃすごい!あんまりこういうの見る機会なかったけど、一気に読んでしまいました。